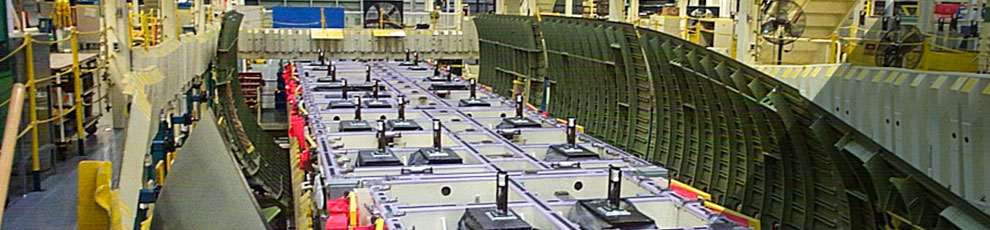
Learjet 85 Final Assembly
AIT was selected by Bombardier to design and fabricate bond molds, assembly jigs, and factory automation tools for the Learjet 85 program in Belfast, Northern Ireland; Queretaro, Mexico; and Wichita, Kansas. The Learjet 85 business jet utilizes substantial carbon fiber in much of the airplane structure, and AIT developed approximately 2,500 tools from carbon fiber and aluminum to produce details and to assemble flight component details.
Belfast, Northern Ireland
AIT produced the carbon fiber and Invar tooling for the Resin Transfer Injection (RTI) process that Bombardier in Belfast utilizes to produce near matched molded carbon fiber wing components including the one piece wing planks. These sophisticated molds produce very repeatable carbon fiber structural components and AIT worked closely with Bombardier to design and fabricate the molds to exacting specifications. These components are then sent to Queretaro for assembly in jigs fabricated by AIT.
Queretaro, Mexico
Bombardier in Queretaro utilizes Out-of-Autoclave (OOA) processes to fabricate carbon fiber components for the fuselage and empennage. AIT designed and fabricated the bond molds for the OOA processes that are used. The forward and aft fuselage sections are built with very large complex multi-piece molds that require assembly and disassembly for each one-piece fuselage section. AIT designed and built tooling that provided a means to do the assembly and disassembly manually in a short schedule window so that fuselage barrel development could occur while an automated machine could be built and installed. AIT designed and built the automated mold assembly and disassembly cell in addition to a fuselage mold rotation cell used to facilitate the fabrication of the one-piece carbon fiber fuselage sections.
AIT concepted designed and built a wide variety of jigs and fixtures used to locate, drill and assemble detail parts to meet specification and rate requirements. Drill plates, subassembly and final assembly jigs are used to assemble small assemblies to assembling complete fuselage sections. Many of these jigs take into account the unique factory material handling needs including the nose cone-to-fuselage join jig.
Wichita, Kansas
Final assembly of the Learjet 85 takes place in Wichita, Kansas. In addition to developing the tooling for these above pre-final assembly locations, AIT also served as Bombardier’s prime project integrator to develop methodologies, designs, and positioning systems to join major components coming from these satellite locations, including:
- Empennage to aft fuselage
- Aft fuselage to forward fuselage
- Wing to body
Each of the joins requires advanced integrated positioning systems, which include:
- Fuselage transportation dollies
- Fuselage stands
- Pylon jacking stands
- Wing positioning sled
- Wing transportation dollies
- HSTAB transportation dollies
- Ballast tools installation of Nose and Engine
- PAX stairways
- PAX mezzanine
- Empennage Platform
- Overwing Entry stairs
- Moving Line Tugs (MLTs)