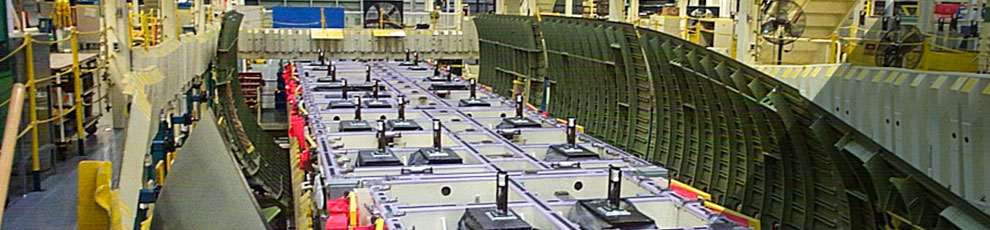
Boeing F/A-18E/F Outer Wing Driller
St. Louis, MO
The multi-mission F/A-18E/F Super Hornet is the U.S. Navy's long-range, all-weather strike fighter, consisting of two variations: the single-seat E and two-seat F models. Replacing the F/A-18C/D, the Super Hornet has, among other changes, a 25% larger wing area than its predecessor.
Boeing selected AIT as their prime contractor / integrator to deliver a turnkey automated drilling system for the F/A-18E/F outer wing assembly. Recent advances in machine design enabled AIT to use smaller, more portable drilling systems for this aircraft. These smaller tools allowed for lean manufacturing techniques to be incorporated into the build process. Boeing benefitted from AIT drilling systems because they require less floor space, provide greater flexibility, and cost less than larger, fixed machine tools.
The AIT automated drilling system was used to automatically drill, countersink, and ream holes in multi-material stacks composed of carbon fiber, aluminum, and titanium in various combinations of each material and thickness. The varying composites can create quality issues, such as burrs, for the aircraft because of their densities, but not with the AIT equipment. For the thousands of holes to be drilled in the F/A-18E/F outer wing assemblies, AIT's automated system sped the process and created more drilling uniformity than previous manual systems.
To make the automation easy to use, the graphical user interface (GUI) on the machine presented in-process data in graphical format as well an NC format. The AIT “scan and correct” feature locating system utilized a spindle-mounted CCD camera to allow for direct indexing of the machine to the work piece. This feature ensured accuracy and save costs associated with templates and human errors.
Innovative Technology
To overcome many of the disadvantages associated with conventional drilling machines, AIT developed and implemented mobile numerically controlled mini-drilling machine. Many of their advantages over traditioinal machines include:
Flexibility – Conforms to various spar configurations regardless of program model or spar hand and can work along entire length of spar
Size – Reduced driller size and maximizes work area while minimizes tooling costs
Ergonomics – Eliminates the need for movement of heavy powered feed drills from hole to hole
Cost Savings – Eliminates need for fixed drill templates saving money associated with their design, fabrication, and maintenance
Reduced Cycle Time and Increased Quality – Provides faster drilling than manual operations; controls variables such as drill speed and pressure; results in greater output
Project Features
- Stationary 5- Axis Drilling Machine
- Right-sized lean manufacturing equipment
- Drill and countersink fastener holes in Outer Wing
- Assembly
- Use “scan and correct” feature to index driller to
- subassembly
- Present drilling data to operator in M&G format and GUI
- Reduce tooling costs resulting from engineering changes
- Increase flexibility and ergonomics