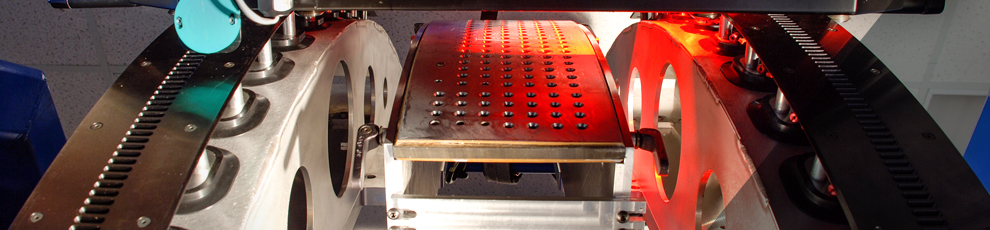
NCDJ
To overcome many of the disadvantages associated with conventional drilling machines, AIT developed and implemented mobile, numerically controlled drilling machines. In fact, a new wing design for the Boeing 767 in the late ‘90s drove the need for AIT to develop its Numerically Controlled Drill Jig (NCDJ).
Historically, drilling fastener holes in large assemblies was accomplished using large machine tools, which were bulky and stationary. Aircraft components had to be delivered to these drillers, creating an inflexible, slower manufacturing process.
Advantages
Many of the advantages of the NCDJ over traditional drilling machines include:
Flexibility - Conforms to various spar configurations regardless of program model or spar hand and can work along entire length of spar
Size - Reduces overall driller size and maximizes work area, while minimizing tooling costs
Ergonomics - Eliminates the need for moving heavy, powered feed drills from hole to hole
Cost Savings - Eliminates the need for fixed drill templates, saving money associated with their design, fabrication and maintenance
AIT NCDJs are small and mobile and possesses extensive computing power to download positions of hole sites and control the positioning of the end effector. The NCDJ conforms to various jig configurations regardless of the program model or position on the wing.
In short, the controller for the NCDJ quickly orients the machine, downloads the hole sites appropriate to the model under construction, and accurately determines the mini-driller's precise location in relation to the work piece.
A graphical user interface (GUI) allows the operator to read the projected position of the hole sites, as downloaded from the Numeric Control Server, off of the GUI and to make ad hoc corrections to the projected hole sites.
See these projects for AIT NCDJ experience:
Additional experience:
- Boeing 767 Stage 2 Spar NC Drilling Machine
- Boeing F/A-18E/F Forward Fuselage NC Drilling Machine