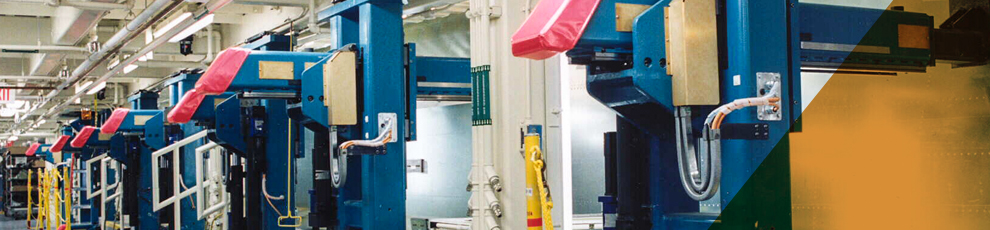
Positioning Systems
AIT has been building precision turnkey automated positioning systems for large aircraft assembly for almost two decades, with more systems operational worldwide than any other company. In fact, the engineering staff at AIT has been involved with almost every large airframe automated control system in the Aerospace industry.
Because of our experience manufacturing hundreds of positioning machines, AIT has been able to develop a standard design for many system elements. AIT can easily modify these designs to exactly match the unique requirements for each project. By using a standard design, AIT provides the shortest lead time and most reliable systems in the industry.
System Elements
With automated positioning systems, AIT has enhanced the Aerospace industry’s ability to manufacture aircraft in less time and with greater exactness and flexibility. Our positioning precision boasts a 0.005” accuracy or better. What gives AIT positioning systems their superior performance is the combination of mechanical actuators (or positioners), control system, and laser measurement system.
The positioners support airplane subassemblies and smoothly move them in a linear fashion as well as rotationally. Each positioner is effectively a three-axis machine whose precision motion is accomplished via servo motor control with resolver feedback.
The automated tool’s control system consists of a high-speed, multiple-axis motion controller and user interface computer. Together, these components synchronize and coordinate the multiple axis moves. An intuitive graphical user interface (GUI) is used to control the system and simplifies the process. AIT’s systems require minimal training while also reducing errors.
AIT’s automated positioning systems incorporate laser measurement technology to facilitate aircraft structure alignment and join. The real-time laser measurement replaces jigs for locating parts and identifies out-of tolerance conditions before errors occur. Real-time part-to-part indexing offers higher tolerance, more flexibility, superior access, and improved ergonomics over traditional hard tooling. This improved method of assembly is controlled through the use of the GUI or joystick, making the system exceeding user friendly.
Benefits
Each benefit of AIT’s positioning systems results in heightened cost containment for our customers.
Speed - Faster tool setup, faster positioning of assemblies, and fewer move iterations to locate the assemblies result in faster flow of assemblies through the factory floor, shorter cycle time, and reduced work in process.
Quality - Unrivalled number of automated positioning machines in the aircraft industry ensures utmost accuracy and precision. Automated positioning produces superior quality final assemblies through tactile subassembly handling and by providing a means to analyze as-built data.
Reduced Direct Labor - User-friendly technology facilitates greater production rates, less overall labor costs, and fewer human errors.
Flexibility - Flexible automation equipment means a lower investment of fixed tooling, shorter lead times if a variation is introduced, and flexibility with production and the facility.
See these projects for AIT positioning system experience:
- Boeing 787 Dreamliner Final Assembly and Body Join
- Boeing 747 FAIT Automated Alignment
- Lockheed Martin F-35 Joint Strike Fighter Final Assembly
- Bombardier Challenger 300 Final Assembly
- Boeing Next Generation (NG) 737 Final Body and Wing-to-Body Join
- CASA DO728 Automated Wing Assembly
- Fairchild Dornier 528, 728, 928 Jet Final Assembly
- Boeing 777 Automated Alignment and Empennage Positioning
- Bombardier Global Express and G5000 Final Assembly