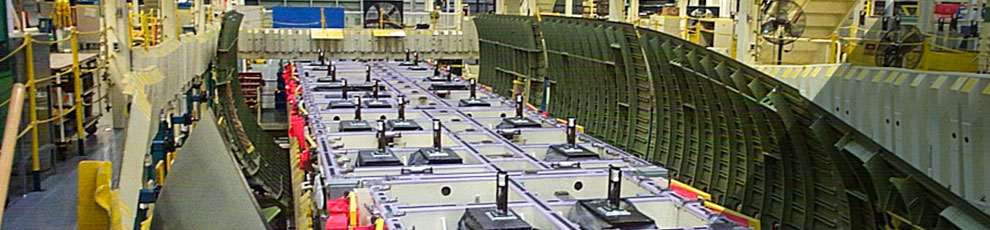
Boeing 747 FAIT Automated Alignment System
Everett, WA
In the mid-1990s, The Boeing Company sought to become more competitive in the commercial airplane marketplace by improving its manufacturing capabilities, while reducing overall production costs. This bold goal resulted in the fuselage assembly improvement team (FAIT), a new technique to completely assemble the 747 fuselage by “snapping” together panels. Together with another earlier ‘90s initiative – accurate fuselage assembly (AFA) – Boeing’s ultimate objective was to achieve a significant cut in assembly flow time over the next several years.
To meet this challenge, Boeing selected AIT in 1999 as their prime contractor for the 747 FAIT Automated Alignment System.
As the Prime Contractor/Integrator, AIT provided a full range of deliverables, including the design, fabrication, installation, test, commissioning, training, and program management for this automated system. For the 747, this entailed two or more panel assemblies being joined together and mated to frames to form even bigger assemblies. Additionally, the system needed the flexibility to build the four required 747 variations: freighter, passenger, and combination models as well as the updated 747-8.
The scope of the AIT project involved automating the measurement and positioning of major structural subassemblies in the Sections 42 and 46 lower lobes and Sections 41/42, 44, and 46 major assembly areas. To accomplish this, AIT used integrated rotating lasers within the positioners to measure section positions relative to the fixed tool targets.
The AIT FAIT automated alignment system included 13 automated fixtures composed of over 200 positioners and approximately 700 axes of servo motion – all under the control of RTCs, AIT's graphical operator interface, mobile joystick, and mobile GUI pendants. Because of its ease of use, AIT equipment enabled the sections to be automatically aligned with the touch of a button.
Innovative Technology
AIT worked with Boeing to develop Determinant Assembly, a new method of indexing parts that simplified the way the aircraft could be put together. The new assembly process ensured commonality of work, which is more adaptable to "lean" manufacturing principles because it uses part-to-part indexing, rather than a conventional part-to-tool indexing system.
The Boeing Company and AIT, as prime contractor, developed and installed automated positioning systems throughout 747 fuselage assembly areas that enabled Determinate Assembly techniques.
Benefits
- Flexibility in assembly tooling with reduced variability between requirements for three aircraft variations
- Assembly accuracy with no panel mismatching
- Ease of assembly and associated speed
- Reduced downtime for tooling maintenance
- Improved shop floor ergonomics
Project Features
- AIT Integrator/Prime Contractor - sole supplier to Boeing
- Automated panel manipulation in 2 Lower Lobe assembly tools
- Automated panel manipulation in 3 major assembly tools
- 13 automated assembly fixtures
- 200 positioners
- 700 axes of servo motion
Achievements
- Met Boeing’s reduced assembly time goal with new Determinant Assembly process
- Instituted laser tracking and part-to-part assembly technology to implement improved manufacturing capabilities and reduced production costs
- Automated the control of over 50 end-effectors in a 15ft x 15ft x 75ft volume