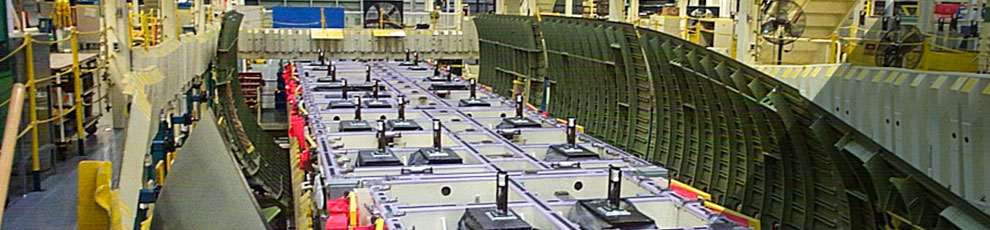
Boeing 737 NG Final Body Join Alignment Systems
Wichita, KS
The most-produced commercial passenger jet in the world, the Boeing 737 is a short- to medium-range, single-aisle, narrow-body jet airliner. To remain competitive in the marketplace with this popular aircraft, Boeing launched the 737 Next Generation (NG) series in the mid-1990s. Boeing focused on its goals of speeding production while maintaining its superior fuselage quality for the five different models.
To help achieve these objectives, Boeing selected AIT as its prime contractor/integrator to provide turnkey laser alignment systems for the 737 final body join.
The AIT alignment system measured and automatically positioned major fuselage components during the final assembly process. In these systems, articulating lasers and airplane-mounted passive targets were used to measure positions and orientations of four fuselage sections relative to the wing stub section. Operators at the console observed the position data and actuated section moves using the touchscreen. The control system performed coordinated linear and rotational moves in and about all three airplane axes, utilizing servo positioning.
AIT provided state-of-the-art controls while directing mechanical, electrical, and panel fabrication subcontractors in the delivery of seven identical tools.
Project Features
- AIT Contractor/Integrator
- Sole Supplier to The Boeing Company
- Positioning of 5 fuselage sections for final join
- Capable of building 5 different models
- 7 final assembly tools
- 140 positioning machines
- 200 axes of servo motion
- Provides technology to speed production
- Provides technology to improve fuselage quality