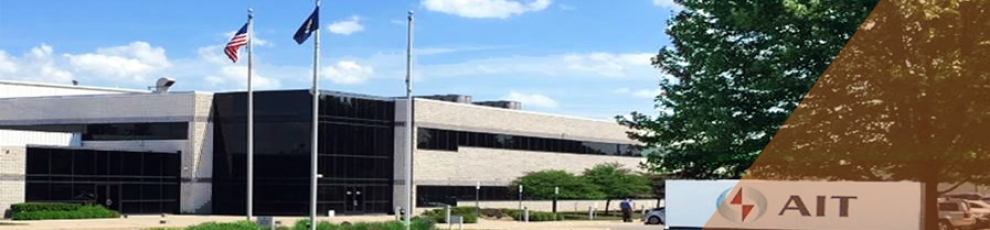
Motion Control System For Boeing 787 Assembly
Advanced Integration Technology (AIT) uses advanced motion controls on Boeing final 787 body join assembly project. It uses a high-level drives platform and motion controller system, failsafe CPU, and distributed I/O, running over Profinet network.
For the Boeing 787, Advanced Integration Technology (AIT) designed and built final body assembly systems needed to join the major fuselage components, plus a moving production line. Key elements in this design included the motion control system, servo drive platforms, failsafe CPUs, and all distributed I/O, with the entire hardware suite communicating over a Profinet network.
As a prime contractor on the 787, AIT had responsibility for the final assembly and body join functions, charged with delivering a fully automated positioning and joining system. In the end, two complete assembly systems and one positioning system were provided. The three main sections of the fuselage are joined, with 14 positioners mounted to transport structures that move either independently or interlocked and indexed to the factory floor for stability. Real-time positioning measurement data are logged with an integrated indoor GPS. AIT designed the alignment and positioning systems to allow rolling them under the aircraft dollies after the sections were brought into the Boeing factory, radically reducing auxiliary equipment needs, materials handling requirements, and additional positioning steps in the overall process.
Motion calculation
On-site at Boeing, the 14 positioning system components were moved into their respective locations near the cradle dollies and engaged to lift and move the aircraft sections. Once the system was rigidly joined, a measurement system onboard located the airplane sections. This information was fed to the AIT system’s software application. From those data points, the system could then calculate how much each section (nose, tail, left and right wings) needed to move to ensure an exact fit to the adjoining section. This precise alignment ensured a smooth and more rapid build of each aircraft’s fuselage.
Ed Chalupa, president of AIT, said he wanted the latest off-the-shelf hardware and software, global engineering support, and training. “Both Boeing and AIT were keenly sensitive to lifecycle security issues in this critical area of the project.” Other important attributes include prototype and demo equipment for AIT use, with ongoing technical support agreements covering products and software updates.
Architecture
The motion control system uses a motion controller, human machine interface (HMI) on a Microsoft Windows-based PC, a PLC for safety, and multiple I/O modules, all on a Profinet network. This basic architecture was then multiplied by the number of control nodes for each specific operational system in the overall production line being designed by AIT. Each unit is capable of working independently of the others in the line. Or, with the addition of relatively few Profinet cables and mode selections on each unit, the final body join assembly tool is able to run as one entity. When running together in this latter configuration, safety devices work in concert, providing proper response levels to all E-stop events on the line. Each unit motion controller receives commands to perform uniform group movements with the tool as a whole via network communications from the HMI.
The motion controller controls all axis movements to accurately position and align parts. Because AIT delivers a turnkey and dedicated system, customers have no need for further internal customization of the controller hardware or HMI panels.
AIT designed the overall layout of the control architecture, programmed the motion system with the PLC, distributed I/O, and integrated safety, plus provided support on the Boeing internal structure and lifecycle support requirements.
Subassemblies split
In the field, the final assembly and body join automated assembly systems, plus positioning system provided to Boeing, are used to join Section 41 (forward fuselage), Sections 47/48 (aft fuselage), and Section 12 (left and right side wings) to the mid-fuselage of the 787 aircraft. Two major subassemblies, namely the forward/aft body positioners and left/right wing positioners, are further split for transport into left- and right-hand minor subassemblies.
AIT designs and manufactures custom tooling and assembly equipment used to fabricate and assemble major commercial and military aircraft. As part of its total value proposition, AIT houses over 500,000 sq ft for engineering, precision metal fabrication, machining, and assembly of its production systems. The company’s equipment is typically used for assembly as well as machining of all the current aircraft structure materials, including aluminum, aluminum alloys, titanium, carbon fiber, Invar, and many specialty alloys and composite substrates.
- Edited by Mark T. Hoske, content manager CFE Media, Control Engineering, Plant Engineering, and Consulting-Specifying Engineer, mhoske@cfemedia.com.