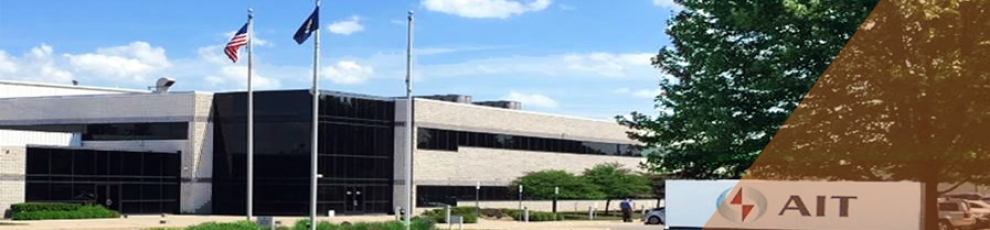
High-Flying Robotics
Traditionally, aircraft assembly has been a labor-intensive, manual process. Large jigs, fixtures, cradles, platforms, scaffolding and gantry systems are a common sight on factory floors. But, robots are slowly becoming a key part of military and commercial aircraft production lines as the aerospace industry adopts new materials, grapples with throughput issues, and addresses ergonomic concerns and skilled labor shortages.
Within the next three years, demand for robotic equipment will increase dramatically because of new technology that addresses accuracy.
Aircraft manufacturers and suppliers are eager to invest in automation to streamline production, increase flexibility and reduce costs. To tackle those challenges, they are using six-axis robots to build airframes, cockpits, engines, landing gear, wings and other subassemblies.
Robots are ideal for repetitive assembly operations, such as drilling, fastening, composite layup and welding. Trimming, routing, painting, coating and nondestructive testing are other applications where aerospace manufacturers are applying robotic technology.
At Spirit AeroSystems Inc. (Wichita, KS), a leading supplier of airframes, robots are currently used in some applications that were previously done manually. “Others are working in applications that were previously thought to require multimillion dollar machine tool automation or extensive tooling and expensive specialized hand tools,” says Curtis Richardson, associate technical fellow for assembly and automation technology.
Spirit AeroSystems currently uses robots on several product lines, including Boeing 787 fuselage, pylon and wing structures; Boeing 737 fuselage and thrust reverser components; Sikorsky CH-53K cabins and cockpits; and Cessna Columbus fuselages.
“We are actively investigating the feasibility of using robotics for a large variety of other applications including fastening, automated fiber placement, friction stir welding, sealing and assembly,” adds Richardson. “While there are many opportunities to make improvements using robotics, we recognize that there are also a tremendous number of complex operations involved in building aircraft that will always need to be people-based.”
It's a Tradition
|
Much of the final assembly for aircraft structures is traditionally done manually using jigs and fixtures because of the mobility required and limited access associated with many of the operations. “Assembly processes in many cases have to be mobile enough to service a structure the size of a large commercial aircraft, yet small and dexterous enough to perform functions in extremely confined spaces within wing structures on smaller civil airframes,” says Rush LaSelle, general manager of western operations at FANUC Robotics America Inc. (Rochester Hills, MI).
Most high-volume aircraft being built today were designed more than 10 years ago. The prevalence of legacy programs is one of the main reasons why robots have not penetrated the aerospace business as deeply as some other market segments, such as automotive and consumer goods.
“The aerospace industry is extremely conservative and the programs are quite long in duration,” says Joseph O’Brien, aircraft group program specialist at Comau Inc. (Southfield, MI). “The technology used in legacy programs tends to be the technology proposed for new programs, as that is what companies are set up for; there are known production capabilities and known costs.
When an aircraft is developed, the assembly processes are created and approved at the same time. Aerospace manufacturers have billions of dollars tied up in fixtures, tooling and large monument systems. Many older tools and processes do not readily lend themselves to automation.
“Once the processes are established and working, manufacturers are reluctant to change because of the expense and the time involved in validating the new process,” explains Dave Masinick, aerospace account manager at KUKA Robotics Corp. (Clinton Township, MI). “[However], manufacturers are looking at more automated assembly for new aircraft being developed.”
“Robots are used more in aerospace manufacturing than is commonly recognized,” adds LaSelle. For instance, his company has already deployed more than 200 robots in the industry.
In recent years, many large aircraft manufacturers have outsourced airframe, cockpit and tail production to suppliers such as Aerolia (Toulouse, France), Alenia Aeronautica (Rome, Italy), Premium Aerotec GmbH (Augsburg, Germany), Spirit AeroSystems and Vought Aircraft Industries Inc. (Irving, TX). “Companies that manufacture subassemblies are increasingly adopting robotic technology,” claims LaSelle.
Those manufacturers see robots as a way to address cost and productivity issues. “While automation can improve throughput, repeatability and quality, the production rate must be high enough to justify the investment,” says Martin Wimmer, head of R&D at Vought Aircraft. “[Despite recent advancements in addressing dimensional accuracy], it is still necessary to run the business case to ensure that your investment in capital will be recouped. In other words, [robotics] needs to earn its way [onto the plant floor].”
“[We consider] robots to be a viable option for many processes now, but each application must be carefully evaluated on a case-by-case basis to ensure that robotics are a good fit in terms of cost, capability and flexibility,” adds Spirit’s Richardson. “Robots will be involved in some way in nearly all of the new work that [we have] won in the last few years.”
Within the last year, Spirit has started two new internal teams to address the increasing interest in robotics. The first is a robotics technology interest group that’s made up of R&D engineers. “The purpose is to provide a regular forum for coordinating development efforts, sharing current project work, and to act as a common resource for discussion and information on topics relating to robotics,” says Richardson. “The group acts as an [internal] technology resource that can be consulted on issues concerning robotic capabilities and processes.”
The second group at Spirit is a robotics steering committee. “Its mission is to define, execute and maintain an enterprisewide strategic plan for the development and application of robotic systems and associated technology,” Richardson points out. This includes oversight of robotic system implementation throughout the company. The group of engineers shares lessons learned and provides expertise and recommendations on equipment capability and standardization.
Reasons for Robots
|
Robots appeal to aerospace manufacturers for several reasons. “The primary reasons are to reduce manpower, increase throughput and improve quality,” says O’Brien. “Also, it reduces the number and cost of hard tools. By augmenting the robot with guidance or localized correction, it can also correct for some as-built variations. A robot can’t make bad parts good, but it can correct for some build variation, whereas hard tooling cannot.”
Unlike gantry systems and other large, heavy pieces of fixed automation, robots can be quickly deployed. “Traditional machinery is very expensive, so payback is sometimes almost impossible,” explains Valentín Collado, head of the mechanical engineering department at Fatronik-Tecnalia (San Sebastian, Spain).
“If the production system is fixed to the floor, it is very expensive and time demanding to reallocate this machinery throughout the shop floor as a consequence of new production needs,” Collado points out. To address that issue, Collado and his colleagues recently developed a portable, three-axis robotic drilling system that is used by Airbus Espana (Madrid, Spain) to assemble wing spars.
“Gantries are technically robots, but they also represent the old way of doing things, as they are generally less flexibile, more expensive and require a special foundation,” adds O’Brien. “The articulated arm robot is the most popular choice due to low cost and high flexibility. But, because of the large size of some aircraft assemblies, they usually require external axes to augment their reach.”
For instance, a seventh axis allows robots to travel up and down large parts such as fuselage panels and wings. “With aircraft, you have to cover a lot of ground,” says Fanuc’s LaSelle. “No robot has the reach to enable it to go from nose to tail on an aircraft. Mobility is an issue that needs to be addressed.” In the future, LaSelle believes more crawler-type robots or automated guided vehicles will be deployed for aerospace assembly applications.
According to LaSelle, the ability to implement one or more robots in place of a custom-designed machine, such as a gantry-based drilling system, takes approximately one-fourth the amount of time, which is a major advantage. “Cost has not proven to be a deterrent to the adoption of robotic technology,” says LaSelle. “In fact, much of the recent activity surrounding the implementation of industrial robotics has to do with the speed with which these systems can be deployed and the significant cost savings associated with using an articulated robot as compared to a custom-designed CNC machine.”
Advanced Integration Technology Inc. (AIT, Plano, TX) has traditionally built stationary drilling machines, positioning systems and other turnkey production equipment for a wide variety of aircraft manufacturers. But, the company has been developing new solutions using six-axis robots. “Within the next year, we will be deploying new robotic systems for drilling and fastening applications, because accuracy, repeatability and vision are coming of age,” says Ed Chalupa, AIT’s president.
Robots also appeal to aerospace manufacturers that are eager to reduce the ergonomic risks associated with repetitive drilling and fastening operations. That’s important, since one single subassembly, such as an air inlet duct on a fighter jet, can require thousands of holes.
Traditionally, parts such as air-inlet ducts and wing boxes require assemblers to crawl into confined spaces. “Wings are internally sealed boxes, and at a certain point in the assembly the box must be closed,” says Ros Conkie, a manufacturing engineer at OC Robotics (Bristol, England). “Ideally, wings should become thinner so these boxes are getting smaller.”
“Automated box closeout has the potential to remove the requirement for manual operators to climb inside the box,” claims Conkie, who has been working with Airbus on an automated wing assembly system using a KUKA robot. “Manual entry is unpleasant and incurs costs associated with compliance with confined-space health and safety legislation. [There’s also the potential for] personal injury claims and damage to composite structures from dropped tools. [In addition], the general awkwardness of the task means that box close out is a slow process.”
Conkie’s company has developed a snake-arm that allows articulated robots to “follow their nose” into a wing to conduct fastening, sealing, cleaning and inspection tasks. The structure of a snake-arm robot is comprised of a number of vertebrae, similar to a human spine.
“It is a tendon-driven arm with wires terminating at various points along the length of the arm—three at the end of every segment,” explains Conkie. “The curvature and plane of curvature of each segment can be independently controlled [using a motor to control the length of each wire].” Control software calculates the necessary lengths of all the wires to produce the desired shape.
OC Robotics has also developed an all-electric swage tool. “It was designed to be used for swaging lock-bolts inside wing-boxes, but is equally suitable for external swaging tasks,” says Conkie. “Historically, hand tools [used in the aerospace industry] have tended to be pneumatic. Electric tools remove trailing services.”
Growing use of composites is another reason why the aerospace industry is eager to use more robots. New all-composite commercial aircraft, such as the Airbus A350 and the Boeing 787, are spurring a need to mass-produce components with complex shapes and dimensions. That demands automated placement tools that can create a wide variety of parts by laying down multiple series of thin composite tapes or fiber sheets.
“The main challenge of fiber placement in aerospace is to reduce the price of the equipment,” notes Clementine Gallet, managing director at Coriolis Composites S.A.S. (Lorient, France), which supplies articulated robots to Airbus and other manufacturers. “Today, machines supplied by machine-tool builders are heavy and very expensive. The machines are so big that you cannot use them to produce parts for helicopters, business jets or regional aircraft. Robots allow flexibility of machine configuration to work on different shapes.”
“With the latest design trends and the use of more exotic materials, aerospace engineers are being called on to explore alternate manufacturing technologies,” says LaSelle. “This has resulted in an increased number of evaluations and tests conducted using industrial robots. The increasingly widespread adoption of composites to lighten airframe components and structures has created new processes [such as fiber lay-up and drilling] where robotics is beginning to play a more critical role.
“Much of the pressure to utilize new materials and design philosophies has created opportunities for airframe manufacturers to rethink how they build planes,” adds LaSelle. “This has, in turn, provided an exciting environment for [robot vendors to] address the challenges and changes by supporting the next generation of aerospace manufacturing.”
Unique Challenges
|
For decades, the auto industry has borrowed ideas from the aerospace industry, such as aerodynamic styling, by-wire controls and lightweight construction methods. But, when it comes to robots, aircraft manufacturers are now looking to Detroit for inspiration.
Of course, building an airplane is completely different than mass-producing automobiles. Aerospace manufacturers face a unique set of challenges that are unheard of in the auto industry, such as low production volumes, exotic materials and large components with complex shapes. Due to the scale of the structures involved, it is also more difficult to achieve full interchangeability of parts.
“The automotive industry has successfully implemented automated assembly by designing cars so that they can be assembled using robots,” says Conkie. “But, in aerospace, weight and aerodynamics take priority over design for assembly. Aircraft assembly is [traditionally] a manual process because the tasks require a high level of skill and dexterity. People are constantly making decisions during the assembly process and adapting to the exact situation.”
High production volumes in auto manufacturing allow engineers to dedicate a robot to a single task, and in some cases, a single component. Aircraft manufacturers are faced with dealing with a high variety of components and tighter precision requirements. The high variety also demands a higher level of offline programming of the robots.
“Automotive production rates average 50 to 60 units per hour,” Comau’s O’Brien points out. “By contrast, a fast production rate for aerospace is one [aircraft] per day, and that day may be comprised of multiple shifts. This can make it difficult to efficiently task a robot for that period of time, as there may be multiple manual tasks that interrupt a given operation leaving the robot idle. This creates potential ‘shared’ work spaces between manual and robotic activities that must be made safe. Such safety generally takes extra floor space, which is usually in short supply, particularly in existing legacy assembly processes.”
There are also extreme volume differences when it comes to parts. “Automotive [suppliers produce] millions per year of the same part, while aerospace manufacturing is in the 100 to 5,000 parts per year range,” notes Patrick Laughter, a regional sales engineer at DENSO Robotics (Long Beach, CA). “The cost of a single aerospace part is typically much higher and the amount of inspection is greater than automotive components. It might take one to eight hours to machine an aerospace component, as compared to one to five seconds per automotive component.”
“Vehicle size and complexity is also a determining factor,” says Mike Beaupre, technology manager at KUKA Robotics. “Typically, [in aerospace] the robot workspace must be significantly larger as compared to automobile production. This can be accomplished through the use of linear slide units, gantry type structures or even mobile vehicles which can transport the robot to accommodate larger workspace requirements.”
“Robots are repeatable but not necessarily accurate,” adds Comau’s O’Brien. “There has been considerable effort by robot manufacturers and integrators to increase the accuracy including multiple encoders, software enhancements, various methods of guidance and localized correction. This is an ongoing process.”
To learn more about robotics in the aerospace industry, click www.assemblymag.com and search for these articles:
• Accuracy Is No. 1 Challenge.
• Aerospace Automation Consortium Touts Robotics.
• Robots vs. Fixed Automation.
• Robots Play a Key Role in F-35 Fuselage Assembly.
• Using Robots Is ‘Just Plane Crazy.
Technology Overview
Advantages of the Flex Track include a lightweight unit for portability, a smaller footprint, and a cleaner factory environment. The Flex Track is scalable for any size aircraft, and contains an intuitive GUI for ease-of-use, fewer human errors, and faster ramp-up.
Austin Weber
webera@bnpmedia.com
Senior Editor