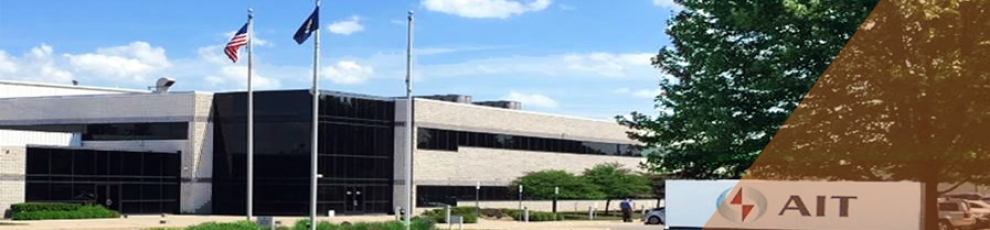
AIT Puts It All Together
A number of suppliers failed to deliver on their commitment to the Boeing 787 Dreamliner program, causing much publicized delays. (The aircraft still had not left the ground as of early September.)
Don’t count AIT (Advanced Integration Technology) as one of the suppliers holding things up. In fact, the industrial automation company already has completed its work with Boeing on the project.
“We had no impact,” AIT President Ed Chalupa recently told Aerospace Engineering & Manufacturing magazine regarding 787 delays. “All of our tools were available. They did not stop one production item. You saw that the airplane rolled out the day it was supposed to. That means our tools were ready and working.”
The airplane that Boeing rolled out in July 2007 was not a finished product, but the structure itself was complete. And assembly of the structure is AIT’s bailiwick. It designed and built two moving join tools that manipulate and align the aircraft sections. The alignment machines and positioning systems are designed so they can be rolled under the aircraft dollies after the aircraft is brought into the factory. The moving tools also accommodate automated circumferential drilling.
In addition to joining fuselage sections, the company’s equipment also is used to join the wing and the horizontal and vertical tail-plane sections to the fuselage. According to Chalupa, AIT has about 85% of the tooling work for the 787 project at Boeing’s enormous plant in Everett, WA.
But the extent of its involvement in the 787 program at Everett is only a portion of what AIT does at the Vought Aircraft plant in Charleston, SC, said Chalupa. In that plant, Vought builds the two most rearward 787 fuselage sections using AIT equipment almost exclusively. The AIT equipment is not just for joining sections; it also is used in the manufacture of the sections themselves. AIT serves as Total Project Integrator for Vought, and as such its level of involvement there is perhaps three times as great as at Everett, according to Chalupa.
Using an unofficial and imprecise measure he calls degree of difficulty—which takes into consideration such things as expenditures, schedule, amount of equipment, and technologies involved—he said Vought ranks No. 1 among all 787 projects that AIT is involved in. Global Aeronautica, for which AIT is project integrator for the mid-and aft-body join and the wingbox mate at that company’s plant (also located in Charleston), ranks second, followed closely by Boeing Everett and Spirit AeroSystems. For Wichita-based Spirit, which produces fuselage section 41, AIT is the main supplier of mandrel assembly and disassembly systems.
“We touch every single piece of that airplane in various stages of assembly, from carbon fiber on a roll all the way to final product,” Chalupa said. “We are the only supplier that deals with every single part of that aircraft in multiple phases.”
A 45-year-old mechanical engineering graduate of Southern Illinois University, Chalupa said the company is seeking new projects and new engineers. The company currently employs about 150 people, including about 80 engineers.
The company has hundreds of automation and drilling systems in operation worldwide and counts among its other major customers Airbus, Lockheed Martin, Bombardier, Embraer, and Northrop Grumman.
The company will be one of many highlighting its capabilities at the Aerospace Manufacturing and Automated Fastening Conference & Exhibition to be held by SAE International September 16-18 in Charleston, SC.
Patrick Ponticel